Rotary packing machines are different. Instead of forming bags from a roll of flat packaging material, this machine is loaded with bags that are already formed into their end shape (premade pouches). The bags are then fed into the machine where they are opened, filled with product, and sealed shut. his package format uses fewer resources to produce than cans or bottles and can be fabricated from recyclable/compostable materials.
Why do we want to use this kind of machine?
Modified Atmosphere Packaging (MAP) technologies, that’s how. From high-barrier packaging materials to nitrogen gas flush to one-way valves, MAP OPTIONS ARE MANY and can be configured to specific product requirements.
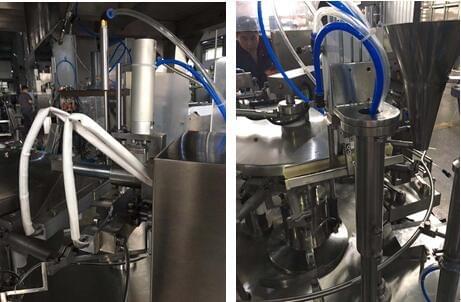
2. A prettier appearance
It stands upright unassisted, acting as its own billboard and enticing customers with an attractive look that screams small-batch quality.
3. Increase capacity
Experienced product packers can fill and seal about 5 - 15 bags per minute. Not bad for a human. But if you reassign this task to a machine, pouches can be filled and sealed at rates of 35 - 60 bags per minute (even more on multi-lane models).
4. Improve quality
A rotary packing machine fills bags with an exact measure of product and creates the perfect seal, every time. No more worrying about under- or overfilling packages
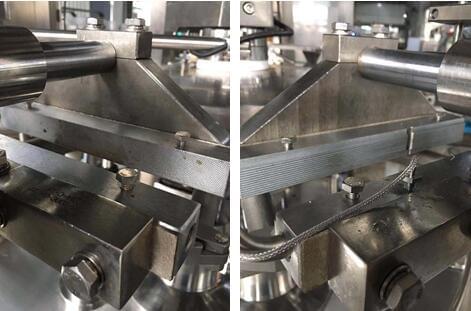
5. Reduce product loss
The product will not dispense if a bag is not detected. In many instances, even during machine setup and changeover, the equipment can be calibrated without running (and wasting) product.